Production Rod Types
Multi-column
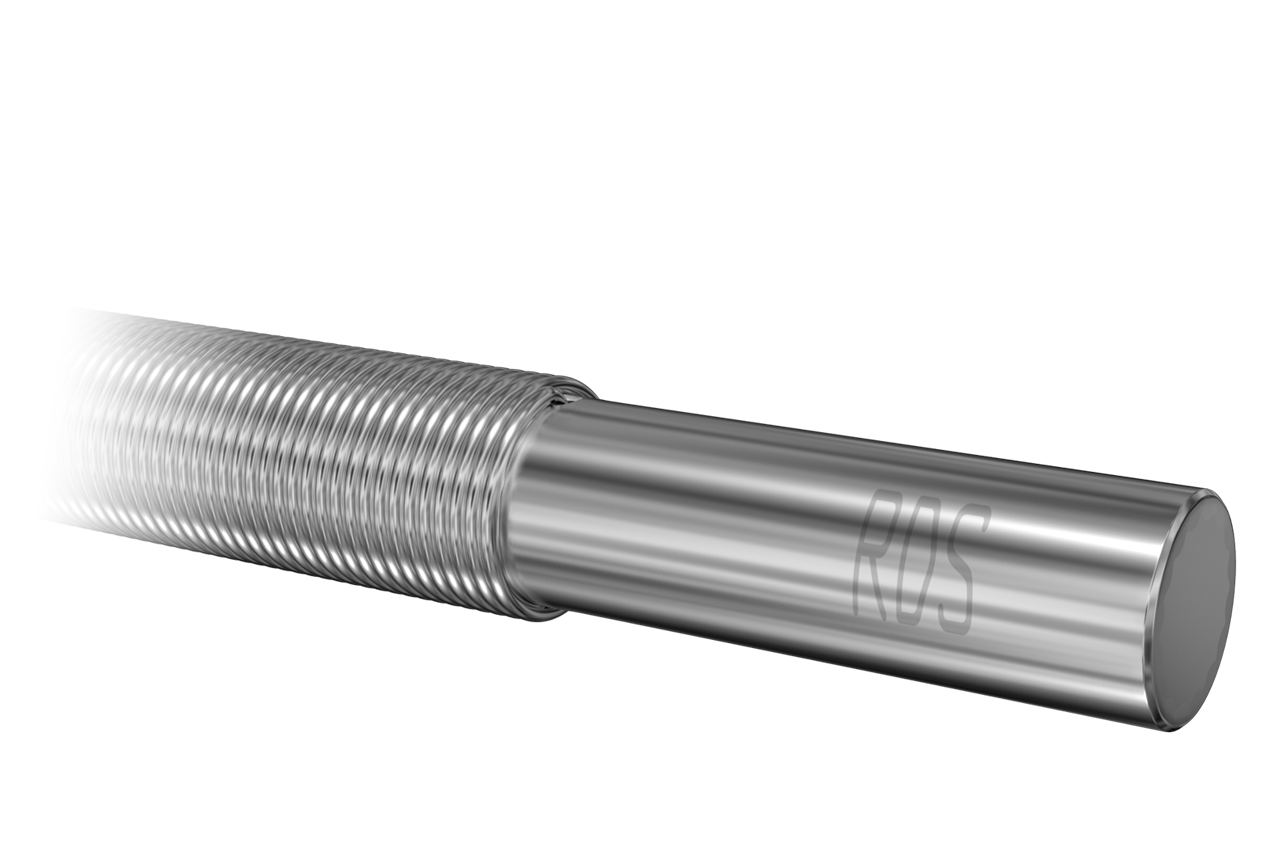
WIRE WOUND RODS
The original “Mayer” rod. Popularized by Charles Mayer in the 1920's and still the most popular. Available in sizes #3 to #75 including many half sizes. The size refers to the wire diameter in mils (.001 inch). Wire wound rods can be stripped and rewound to save cost and reduce waste. There are no minimums and no setup charges for wire wound rods.
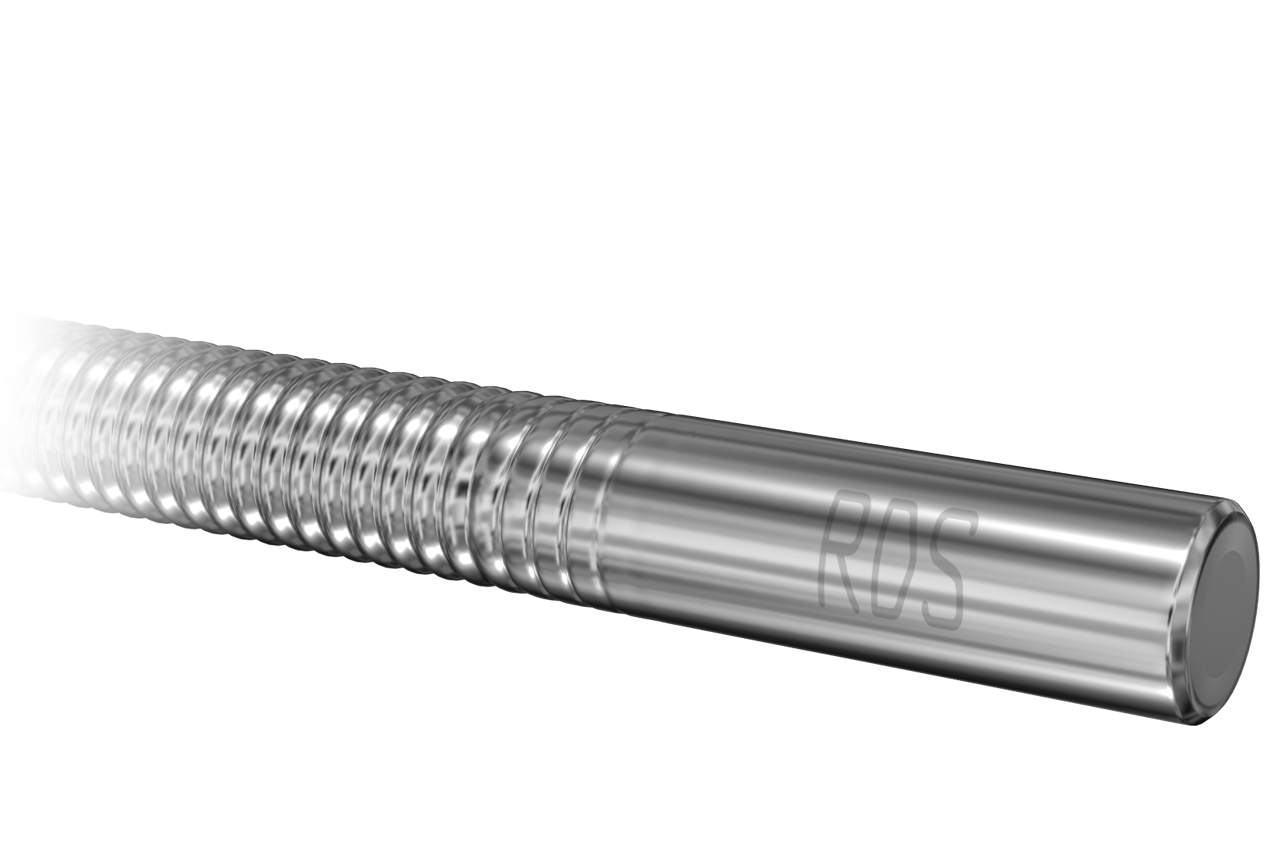
Formed rods
A formed (threaded, grooved, etc.) rod is roll formed from a solid steel bar and closely resembles a wire wound rod. The size of the groove determines the coating thickness the same way the cavity between wire winding does. However, the radius in the groove of a formed rod is less likely to clog and cleans up easier than its wire wound equivalent.
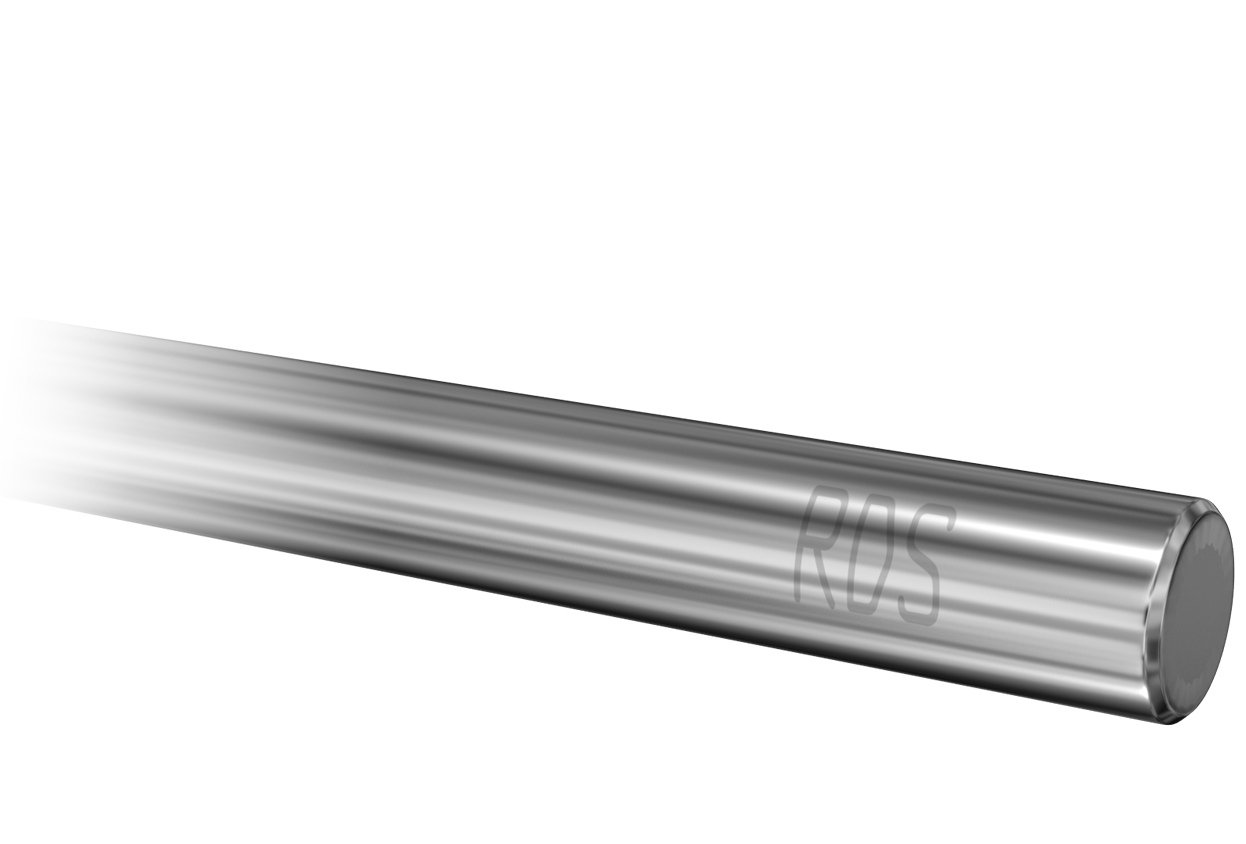
SMOOTH RODS
Commonly used to smooth previously metered coatings to paper, paperboard and plastic films. The coating thickness is governed by pressure (against a backer roll) or web tension. RDS smooth rods can be ground to meet any surface finish requirement and hard chrome plating can extend rod life significantly.
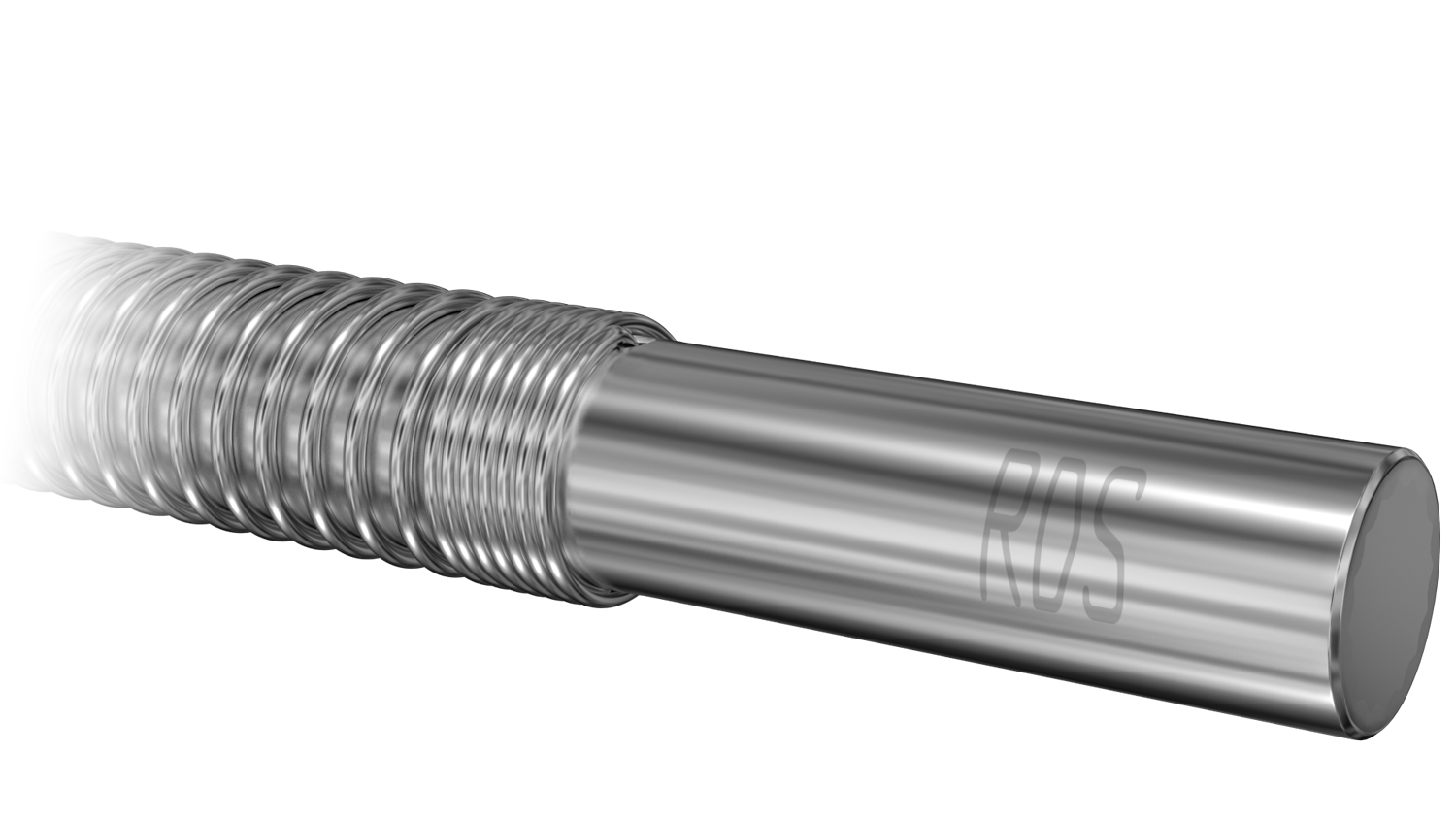
GAPPED RODS
For higher viscosity coatings, gapped rods reduce clogging and eliminate lines. By winding a smaller wire with spacing (see image) the cavity created is wide and shallow allowing heavy coatings to flow better. A smaller wire creates a smaller interruption in the coating flow enabling the coating to wet out more completely. While a gapped rod is less durable than a double wound rod, it is also less expensive.
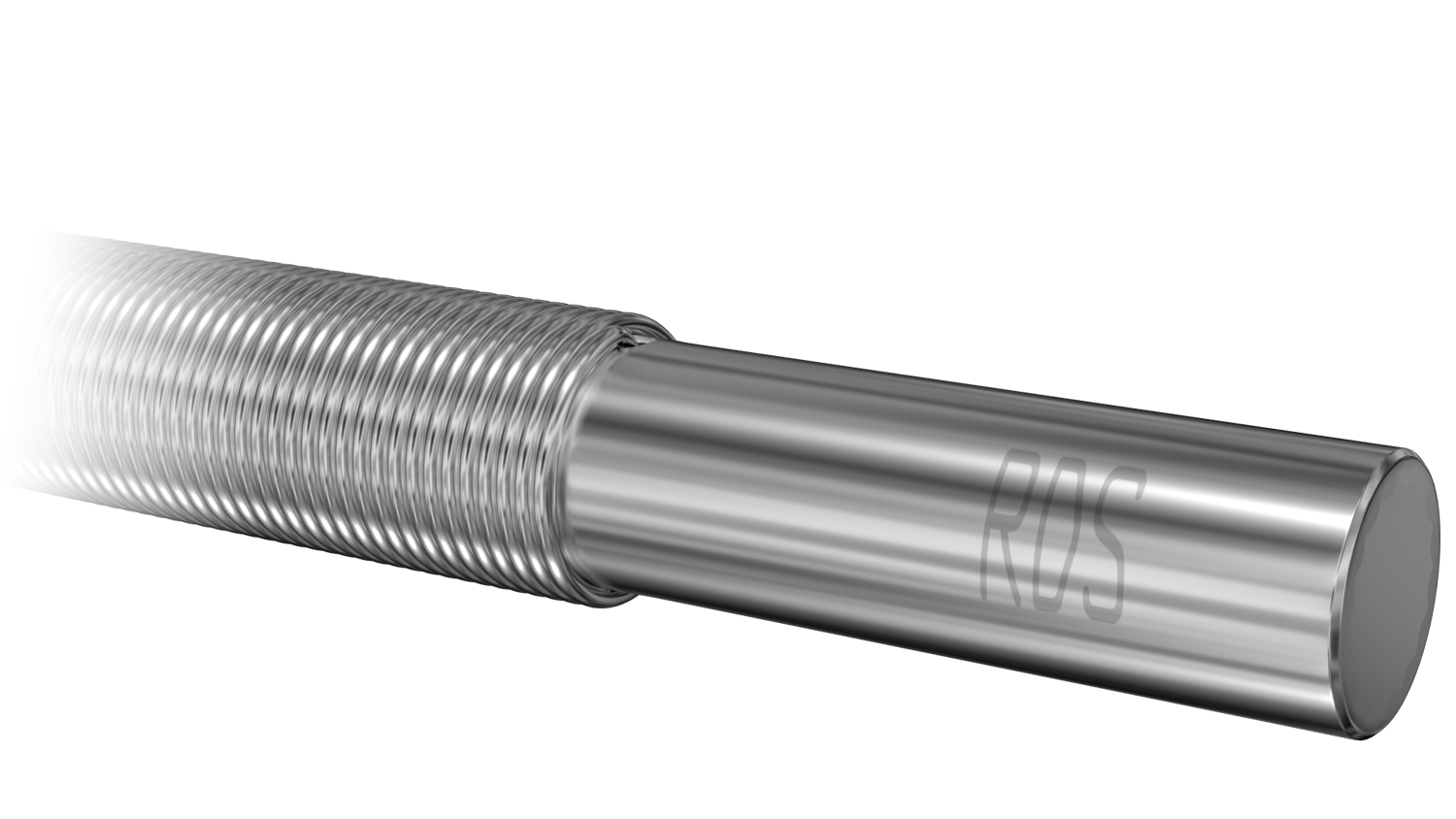
DOUBLE WOUND RODS
For higher viscosity coatings, double wound rods reduce clogging and eliminate lines. By winding a smaller wire on top of a larger one (see image) the cavity created is wide and shallow allowing heavy coatings to flow better. A smaller top wire creates a smaller interruption in the coating flow enabling the coating to wet out more completely. While a double wound rod is more expensive than a gapped rod, it is also more durable.
India
132 Princess Street, Govind Bldg., 2nd Floor
Mumbai - 400 002
India
Tel: 91-22-2203 6216
Fax: 91-22-2208 1346
sales@khushbooscientific.com
www.khushbooscientific.com
COMMON COATER CONFIGURATIONS
Multi-column
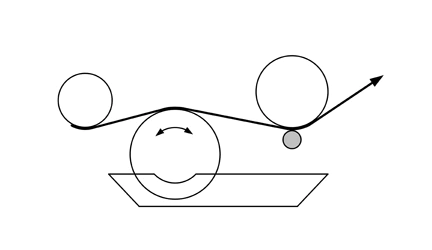
SINGLE MAYER ROD
Most Common
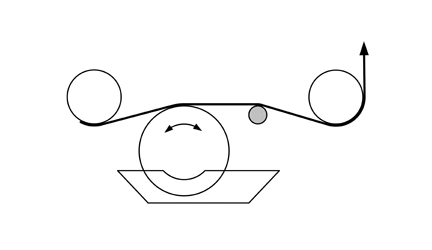
MAYER ROD WITH BACKER ROLL

DUAL MAYER ROD
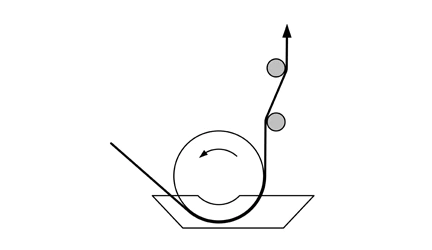
TWO-SIDED CONFIGURATION
SIZE SELECTION
Click a button below for the size selection chart in PDF. Because actual transfer rates are affected by coating rheology, substrate and other variables, this chart is only intended to provide a good starting point for trials. Actual transfer rates can also vary between rod types since the shape of the profile can have a significant effect on coating flow. Also note that the dry coat weight calculations assume a coating density of 1.0 g/cm3.
PRODUCTION ROD FAQ
Multi-column
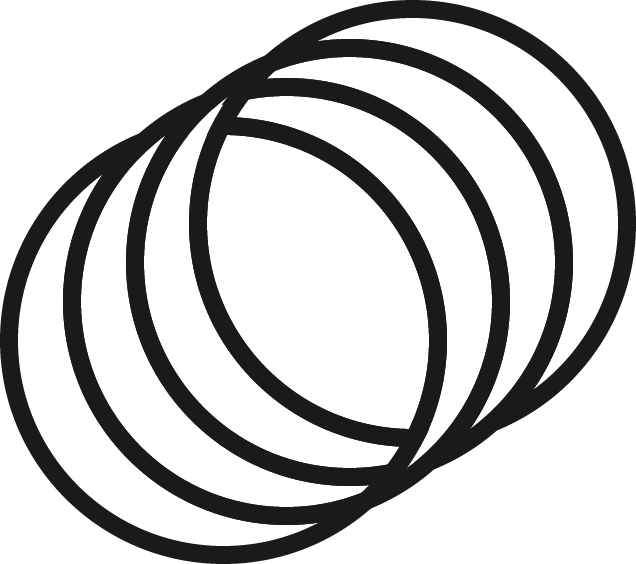
WHAT ARE THE BENEFITS OF MAYER ROD COATING?
Rod coating provides excellent accuracy and uniformity through a wide range of speeds at a low cost that is simple to setup and change over. Mayer rod coating has been and still is in the top three most popular coating methods.
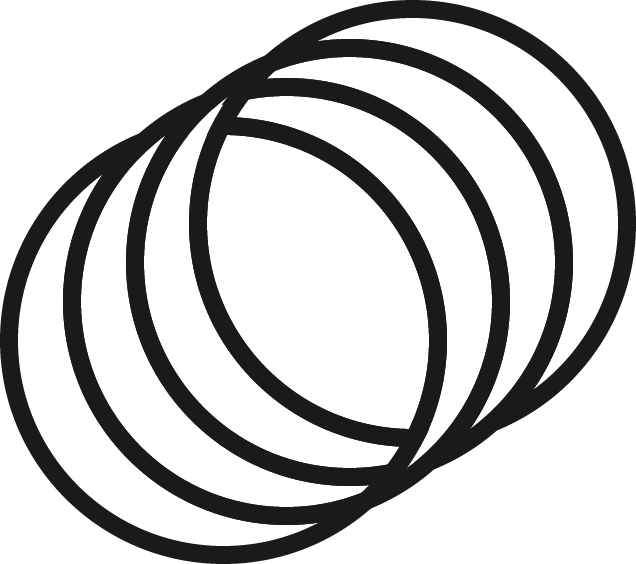
SHOULD THE ROD BE DRIVEN?
Yes, rotating the rod will prevent uneven wear. Rotating the rod will also present a relatively clean rod surface to the substrate.
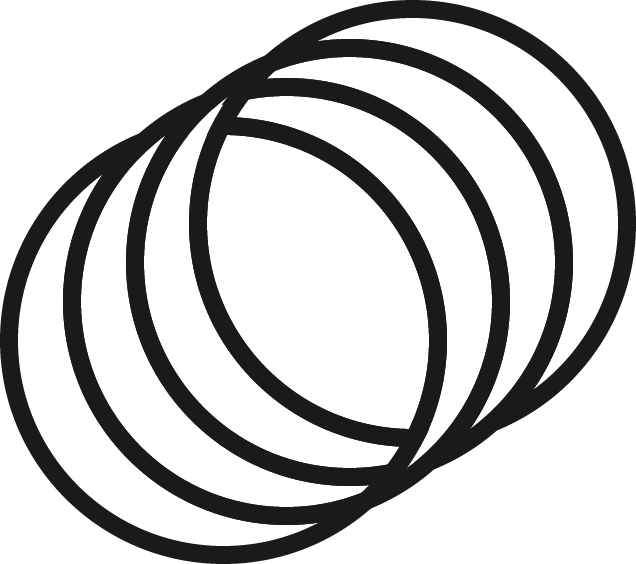
WHICH DIRECTION SHOULD THE ROD ROTATE?
Normally the rod rotates against the web. However, rotating the rod with the web may result in a better finish for some coatings.
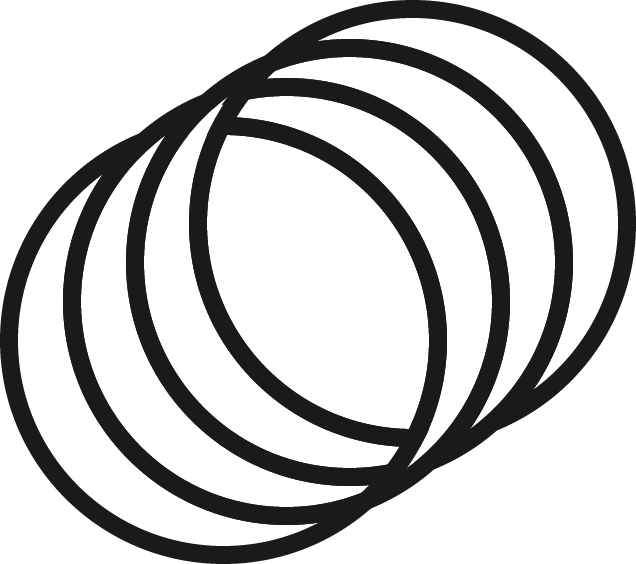
WHAT SPEED SHOULD THE ROD ROTATE?
25 to 50 rpm is a good starting point. Rotate the rod faster to see if the coating finish improves.
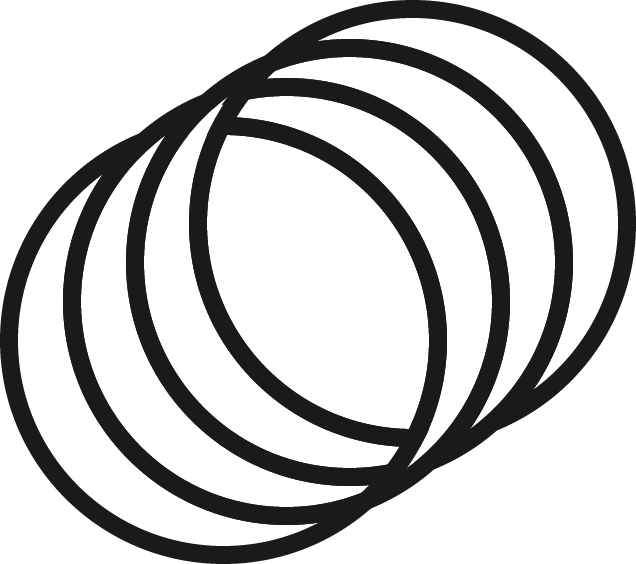
WHAT IS THE BEST WRAP ANGLE?
Every application is different but most coaters operate with 5 to 15 degrees of wrap. The most flexible coaters will be able to adjust the wrap angle for different applications.
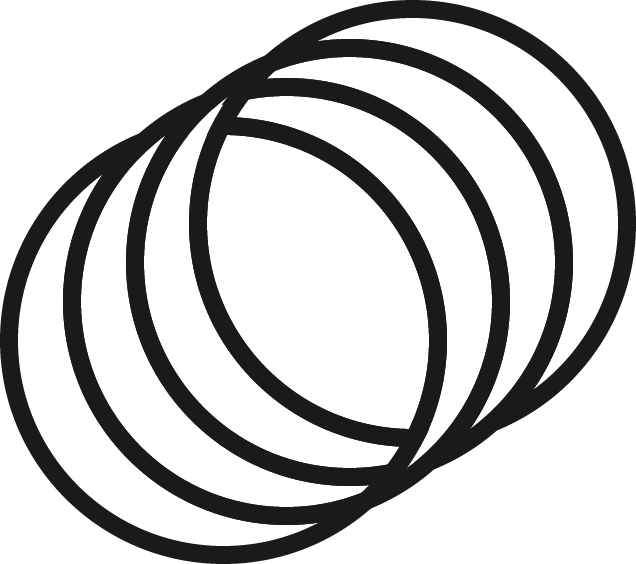
SHOULD I REALIGN THE DRIVE MOTOR WHEN CHANGING WIRE SIZES?
Yes, if the size change is significant enough to prevent the rod from laying flat on the rod bed. (Note that with a 60 degree V-groove rod bed, any increase in diameter will cause an equal increase in rod height).
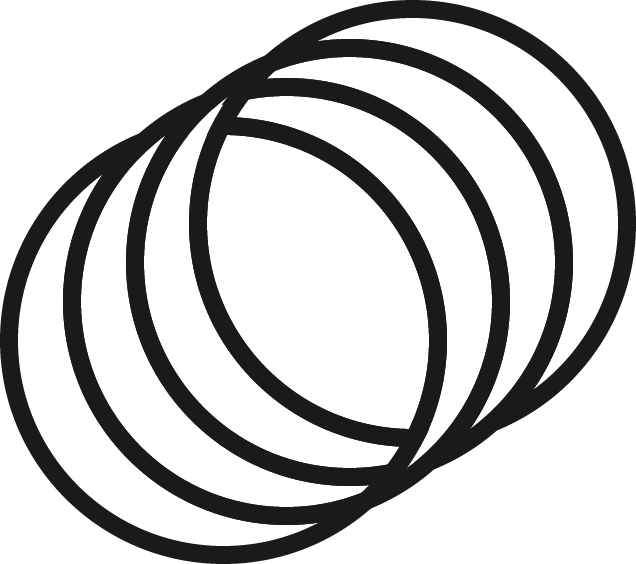
WHAT ARE THE BENEFITS OF FORMED RODS?
The U-shaped groove of a formed rod cleans up easier than its wire wound counterpart. Unlike wire wound rods, the diameter of a formed rod increases very little from a small groove size to a larger one. Formed rods are generally less expensive at high volumes.
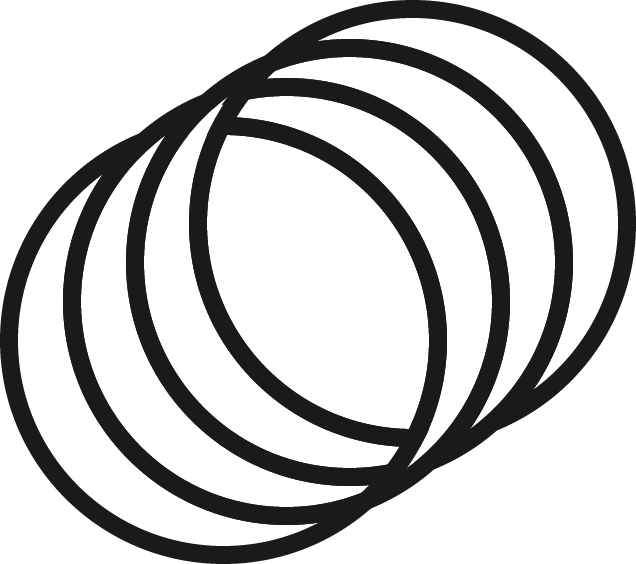
WHY IS THE FILM THICKNESS DIFFERENT FOR A WIRE WOUND VERSUS A FORMED ROD?
The cavity between wire windings is a V-shape while the formed rod has a U-shaped groove. Coating flows through the shapes differently so the actual transfer rate depends largely on coating rheology.
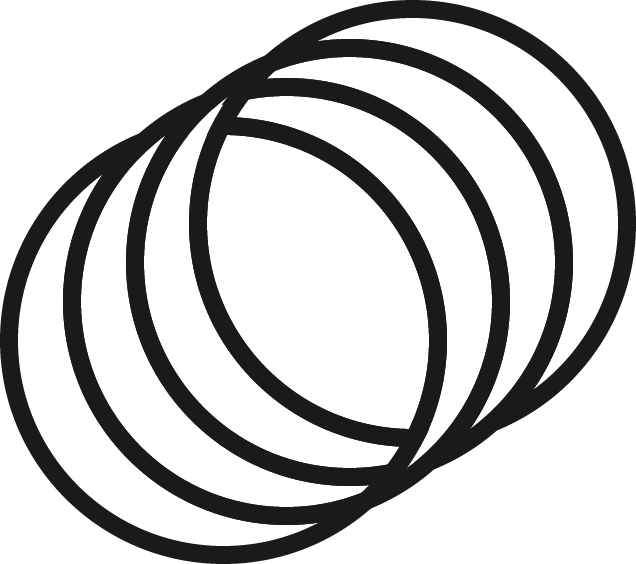
WHAT EFFECT DOES ROD DIAMETER HAVE ON COATING THICKNESS?
None, the coating thickness is determined by the wire (or groove) size.
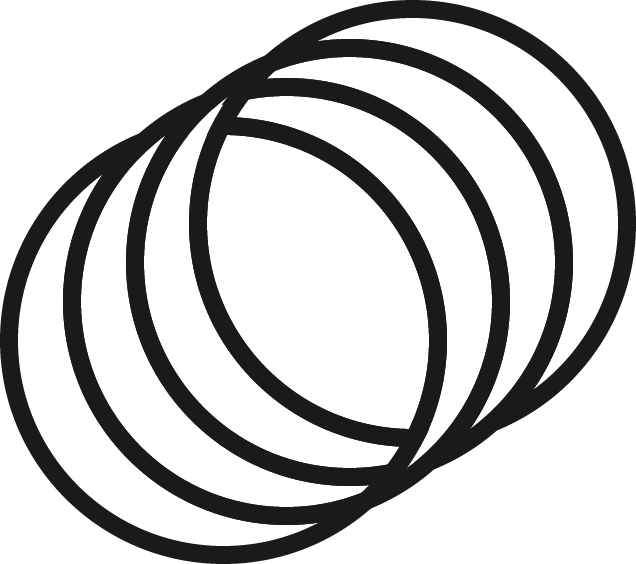
WHAT OTHER FACTORS SHOULD BE CONSIDERED WHEN CHOOSING ROD DIAMETER?
Since rods are generally made of solid stainless steel, the rod diameter will have a drastic effect on rod price. The need for a rod holder depends upon rod diameter (and several other factors).
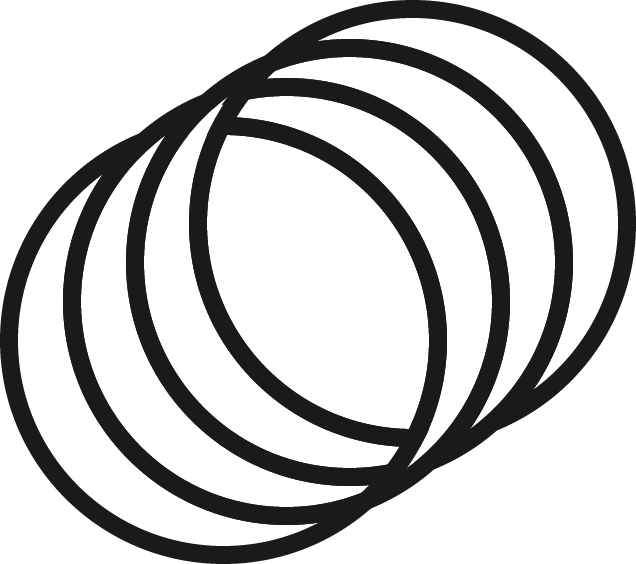
HOW DO I CHOOSE THE CORRECT WIRE SIZE?
Use the size selection chart to find an appropriate starting point. Perform a test with that size (in the lab preferably) and measure the actual film thickness. Use the actual transfer rate (wire size to film thickness) to refine your size selection.
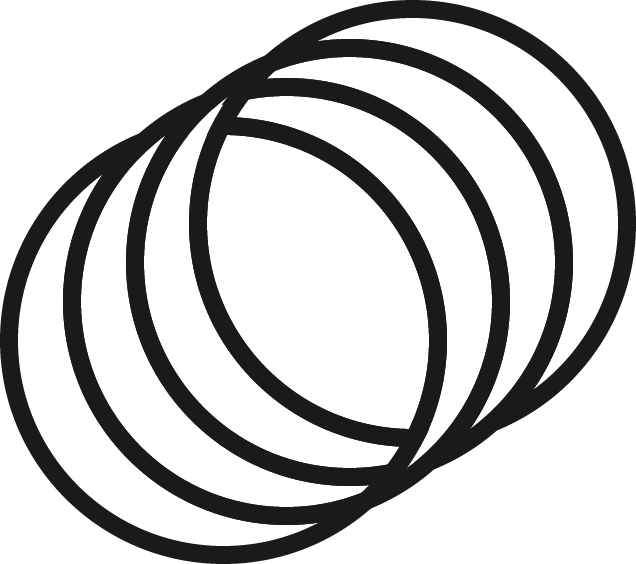
IS THERE A MINIMUM ORDER AMOUNT?
There is no minimum for wire wound rods. There is a 5 rod minimum per size for formed rods (or a $35 setup charge per size).
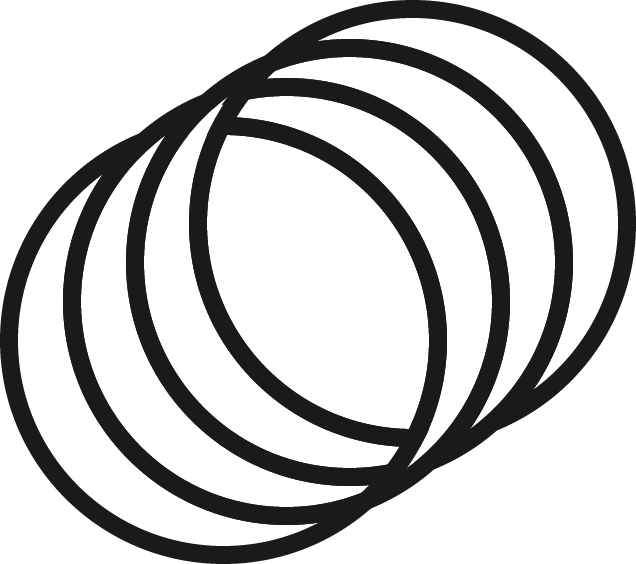
WHAT IS THE STANDARD LEAD TIME FOR CUSTOM COATING RODS?
Our standard lead time is 1 to 2 weeks after receipt of order. We offer stocking programs for higher volume users. If you need an order sooner please contact us about expediting.
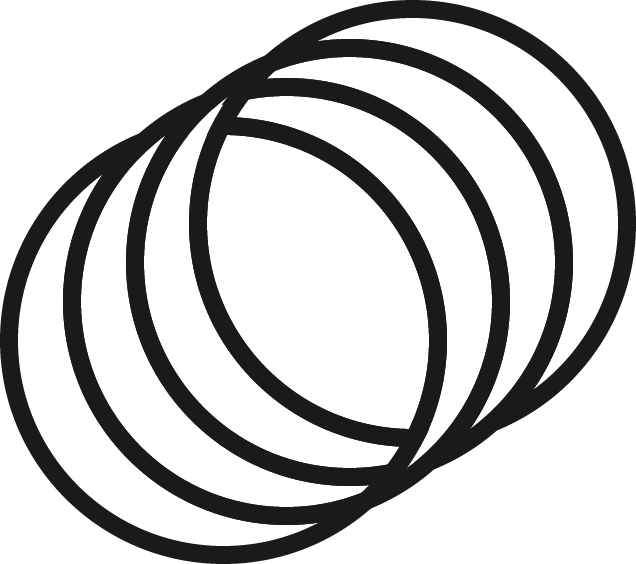
WHAT CAUSES LINES IN THE COATING THAT MATCH THE ROD PROFILE?
The most common cause is a high viscosity coating that will not wet-out. Add a surfactant to the coating or increase the time between coating and drying if possible. If not, consider an alternate rod type, such as gapped or double wound rod.
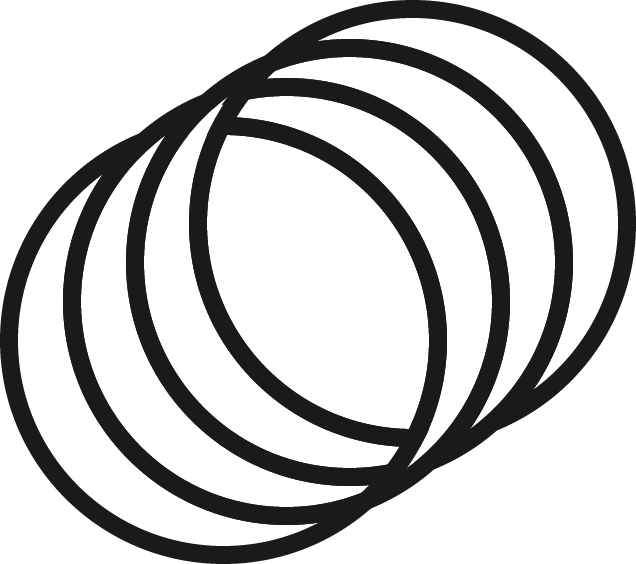
WHY DO STREAKS IN THE COATING APPEAR RANDOMLY OR IN A REPEATING PATTERN?
The rod is likely clogged with dried coating or some other contaminant. Make sure the coating is pumped through a fine enough filter. Rotating the rod also helps evacuate any particulates. The rod needs to be cleaned anytime coating has been allowed to dry on it.
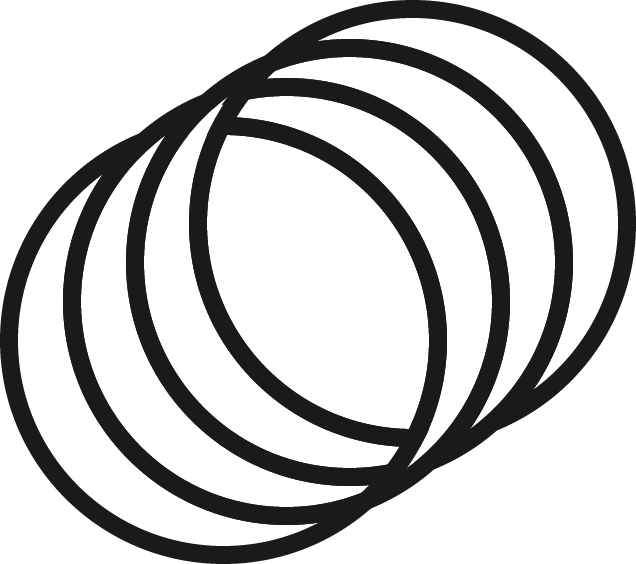
WHAT IS CAUSING THE RODS TO WEAR OUT PREMATURELY?
The life of a coating rod depends on the abrasiveness of the coating and substrate, the hardness of the rod and how well it's maintained. Either the tops of the wires will wear down from abrasion or the grooves will clog up with coating. If the rods wear out consider chrome plating. If the rods clog up consider an alternate rod type. Check the pressure between the rod and the backer roll (if applicable).
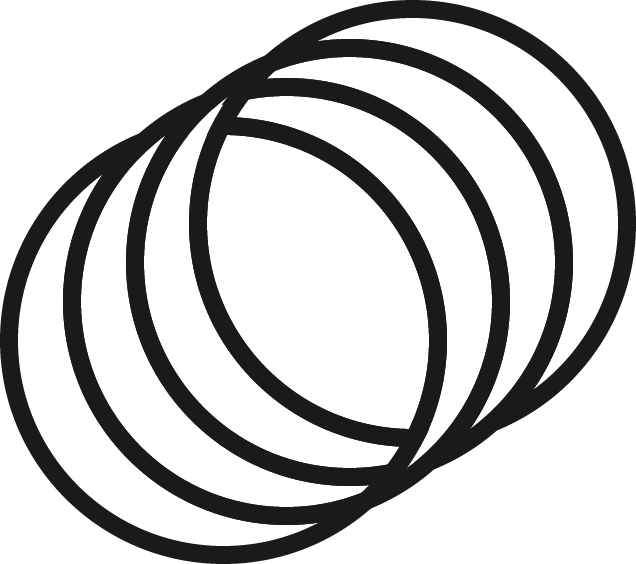
WHY ISN'T THE COATING UNIFORM ACROSS THE WEB?
Check the web tension across the rod (if applicable). Ensure that the rod is aligned with the backer roll (if applicable). Check the straightness of the coating rod and replace if bent.